Agrandissement d’une unité de production pour doubler sa capacité
De renommée mondiale, une production biopharmaceutique nous a sollicité pour son évolution. Elle développe des médicaments hautement innovants en concentrant ses efforts de Recherche & Développement dans 4 domaines thérapeutiques : l’oncologie, les maladies rares, les neurosciences et la gastroentérologie.
C’est sur son site de production en Suisse romande que ce projet ambitieux et d’envergure a eu lieu.
La problématique : doubler sans arrêter de produire
Notre client souhaitait doubler la capacité d’une de ses lignes de production de médicaments via la création d’une extension au sein de son site actuel et l’ajout de nouveaux équipements nécessaires à son bon fonctionnement. À partir d’une page blanche, nous avons accompagné l’entreprise depuis la définition du concept jusqu’à la qualification.
Pendant toute la durée des travaux, ce projet a nécessité une organisation millimétrée et une attention à chaque instant pour faire cohabiter jusqu’à 70 personnes dans un même espace. En plus du défi logistique, il a fallu intervenir sur site dans un laps de temps très court afin de minimiser la mise à l’arrêt de l’usine qui s’est étendu d’avril à septembre 2023. Une telle exécution demande généralement un temps d’arrêt d’une dizaine de mois : nos équipes sont parvenues à l’écourter de 4 mois !
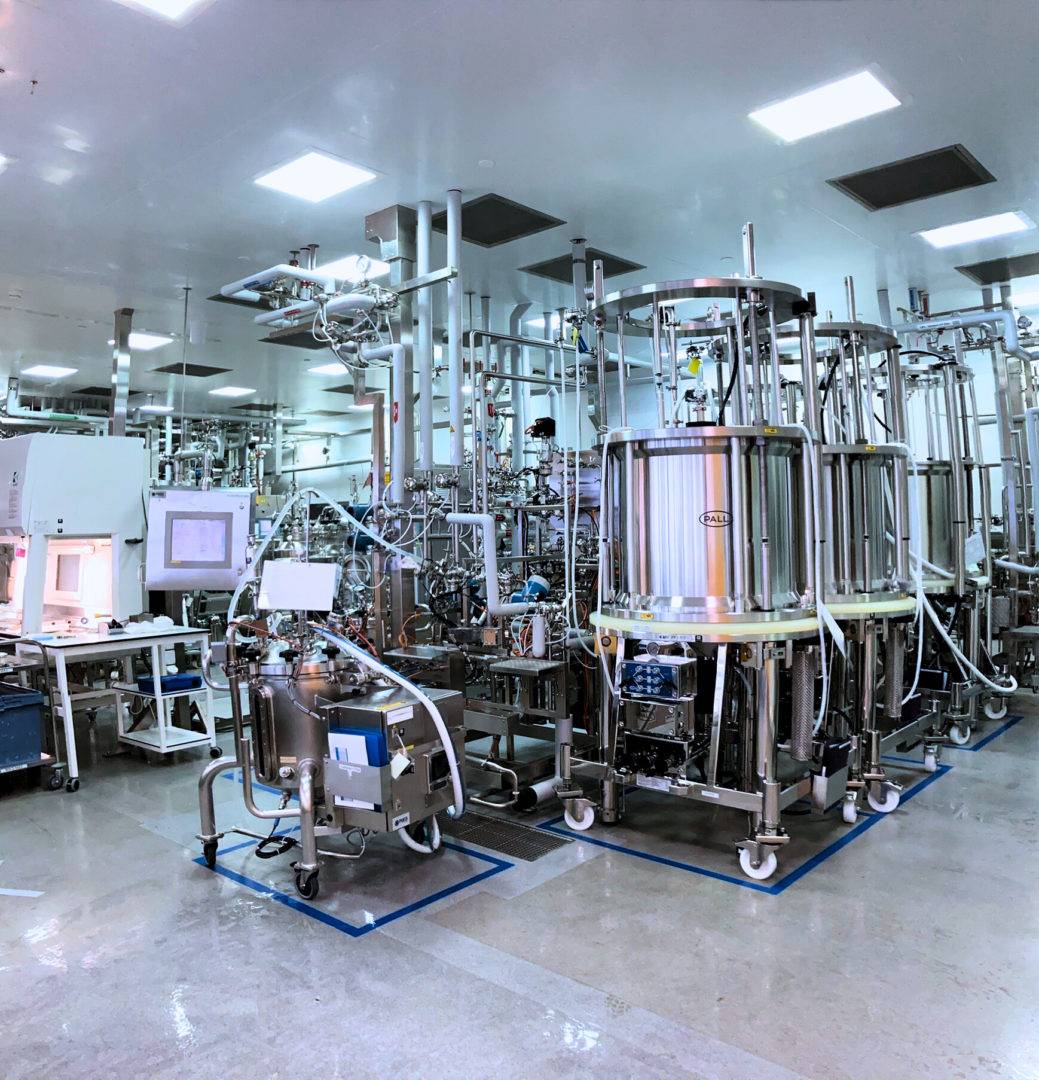
”« Nous avons réussi à tenir les délais demandés et les budgets annoncés lors des étapes de Concept et Basic design. Cela nous a demandé d’être proactifs mais aussi d’apprendre à gérer le stress et la pression. Ce fut un projet très formateur pour nos équipes que ce soit au niveau de notre organisation en interne ou dans nos relations avec les différents intervenants. »
Damien KozuchowskiChef de projet, SP Groups
Les étapes du projet :
- Étape 1 : Les études - Comment tout anticiper ?
- Étape 2 : Utilisation d’outils de pointe avec le BIM
- Étape 3 : Un chantier, c’est une équipe !
Comme tout projet, celui-ci a commencé par une longue phase d’étude, qui a commencé dès le deuxième semestre 2021, jusqu’au début du shut-down (mise à l’arrêt), en avril 2023. Ces nombreuses phases qui ont suivi (Concept Design, Basic Design et Detailed Design), ont rassemblé de nombreux corps de métier dans nos équipes :
- Des ingénieur·e·s process pour le design et dimensionnement de la tuyauterie et des équipements, ainsi que pour le design des salles propres
- Des ingénieur·e·s CVC (Climatisation, Ventilation, Chauffage) pour le design des cascades de pression, des centrales de traitement d’air et du réseau de sprinkler
- Des ingénieur·e·s automaticien·ne·s et électricien·ne·s pour la conception et l’intégration du système de monitoring et de sécurité incendie ainsi que des armoires électriques
- Des dessinateur·rice·s/projeteur·se·s pour les plans et P&IDs et la réalisation de la maquette 3D
- Des managers et coordinateurs BIM pour la réalisation et le suivi des maquettes
En collaboration étroite avec les équipes du client, une stratégie de qualification particulière a également été mise en place en parallèle de ces études.
Ce projet ambitieux s’est immédiatement placé sous le signe de la collaboration et de la co-activité. Les équipes SP Groups ainsi que les nombreux autres intervenants (architectes, ingénieurs civils, ingénieurs AEAI (Etude incendie, etc.) ont travaillé ensemble durant ces mois d’études afin de mettre en lumière les différentes problématiques.
Une fois tous les besoins clairement définis, une phase de « Procurement » (appels d’offres) a eu lieu, durant laquelle des cahiers des charges ont été rédigés en vue d’effectuer les appels d’offre aux fournisseurs et les comparatifs, avant de passer à l’étude d’exécution et à la réalisation.
En amont du chantier, l’équipe BIM a mis en place une charte BIM permettant de définir les règles de modélisation et, à terme, l’aménagement de la zone de production. Le but était de faciliter la coordination et la collaboration entre les intervenant·e·s, tout en faisant émerger d’éventuels conflits entre les corps de métier. Le LOD (Level Of Detail = niveau de détail) 400 de la maquette numérique a permis d’entrer dans un niveau de détail élevé (vannes au boulon près), avant de valider les études (opérabilité, maintenabilité) aux côtés des équipes d’ingénierie, de production et de qualité du client.
Pendant le chantier, un point était effectué chaque matin pour assurer la bonne coordination de tou·te·s les intervenant·e·s, garantir le bon phasage des interventions et éviter les mises en danger.
Une fois la réalisation terminée, le commissioning et la qualification (mise en service, avec des phases de tests documentaires et dynamiques) des installations ont été effectués en partenariat avec le client, afin de préparer le tout pour la production.
Les milestones (jalons) du projet ont été fixés dès le début, 2 ans avant l’arrêt !
- Septembre 2021 à mars 2023 : phases d’étude
- Juillet à décembre 2022 : construction de l’extension (bâtiment auto-porté afin de pouvoir effectuer tous les travaux préliminaires sans mettre en arrêt la production)
- Décembre 2022 à mars 2023 : travaux préparatoires dans l’extension
- 3 avril 2023 : début du shutdown (début du chantier)
- Avril à juillet 2023 : liaison de l’extension au bâtiment existant, réalisation des travaux (résine, cloison, réception d’équipement, tuyauterie, ventilation, …)
- Juillet à mi-septembre 2023 : remise en service et qualification des équipements en collaboration avec le client
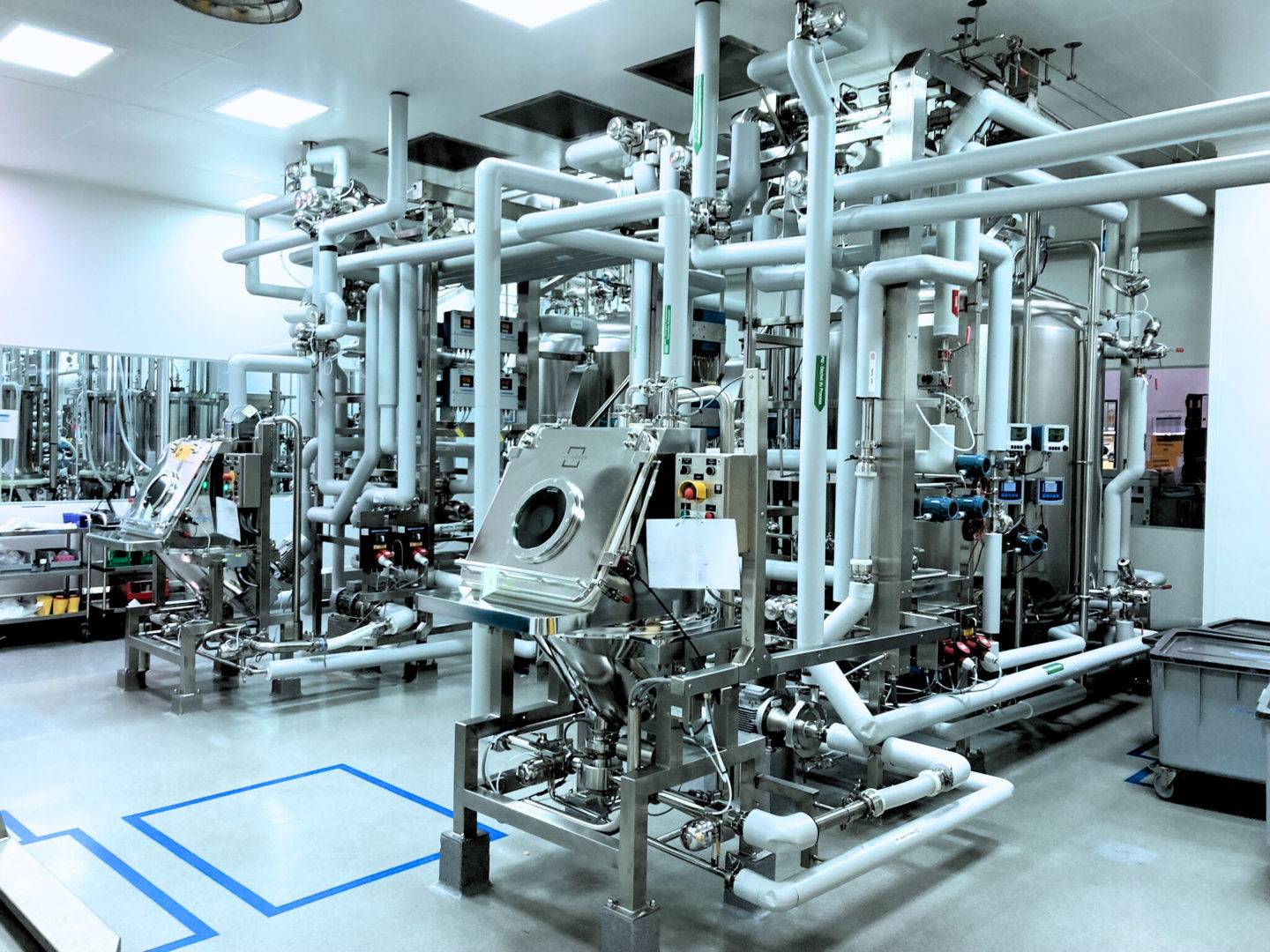
La solution apportée : préfabriquer et construire en temps masqué
Accolée aux locaux de la ligne existante, une extension de 250 m2 sur 3 niveaux a été construite afin de doubler les équipements critiques (colonnes de chromatographie, skids de séparation par exemple) et augmenter la production. Pour SP Groups, le plus grand challenge a été de coordonner l’ensemble des équipes sur le chantier et de sécuriser chaque intervention, tout en maintenant les délais que ce soit pour le revamping du bâtiment existant ou pour la zone neuve. En interne, ce projet a aussi été significatif nécessitant la mobilisation de 35 collaborateurs SP Groups au plus fort de la réalisation.
En co-construction avec les directions techniques de notre client, plusieurs éléments ont requis une attention particulière :
- Il a fallu repenser tout le système de la ligne de gestion de l’eau pour injectables EPPI (véritable colonne vertébrale des lignes de production biotechs) car elle n’était pas dimensionnée pour pouvoir répondre aux nouveaux besoins. Ce challenge a permis de repartir à zéro avec un système plus performant : l’ancienne ligne a été entièrement démantelée, tandis qu’un nouveau système de distribution, incluant toutes les nouvelles lignes, a été conçu et installé. Nos équipes ont dû faire preuve de sang-froid et d’une grande précision pour répondre aux exigences du client en termes de température, de débit et de qualité de l’eau.
- Les clean utilities (fluides ultra-propres) ont dû être intégrées au milieu du process existant. Il a fallu trouver la bonne place et les bons encombrements, au millimètre près et souvent dans des endroits exigus.
- La ventilation a également nécessité l’intervention de groupes de travail pendant plusieurs semaines pour garantir une mise en service optimale entre le système existant et la nouvelle version.
- Certains équipements n’ayant pas été réceptionnés avant le début du chantier, il a fallu suivre minutieusement les étapes de FAT (Factory Acceptance Test) chez le fournisseur, les modifications et les réceptions sur site afin de ne pas impacter les plannings d’exécution.
Lors de la réalisation, les équipes sont intervenues sur plusieurs niveaux. Au sous-sol, quelques équipements et des cloisons pare-feu ont été installés. Au rez-de-chaussée, toute la zone de production a été optimisée et redimensionnée. Dans l’interstitiel (zone entre les faux-plafonds et l’étage supérieur), la mise en place des cheminements et des distributions a demandé une grande vigilance, cet espace étant étroit et soumis à des températures élevées (surtout en été). Enfin, la zone technique a accueilli de nouvelles centrales d’air et armoires électriques ainsi qu’un nouveau skid de nettoyage en place (CIP).
Chiffres clés : des kilos de café !
Jusqu’à 35
collaborateur·rice·s SP Groups mobilisé·e·s
250 m2
d’extension
600 m2
au total (y compris le revamping de la zone existante)
> 4’000 lignes de tâches
à effectuer sur le planning
10 équipements majeurs
ajoutés
> 3’100 mètres
de tuyauterie installée
> 1’800 amovibles
vannes, instruments, clapets, etc.
4 nouveaux automates
et 9 automates modifiés
Près de 2’000 livrables
schémas, plans, spécifications techniques et fonctionnelles, rapports, protocoles de tests, maquettes, etc.
SP Groups et ses équipes sont très fiers d’être parvenus à maîtriser parfaitement le planning et les budgets initiaux.
Ces prouesses techniques et humaines méritaient d’être partagées !
Vous avez un projet dans la biotech à nous confier ?
Discutons-en ensemble !